Arduino Nano - Rotary Encoder
This tutorial instructs you how to use the rotary encoder with Arduino Nano. Here's what we'll cover:
- How the rotary encoder works
- The difference between a rotary encoder and a potentiometer (another type of knob)
- How to connect the rotary encoder to an Arduino Nano
- How to write code for the Arduino Nano to read the direction and position from the rotary encoder.
Hardware Preparation
Or you can buy the following kits:
1 | × | DIYables Sensor Kit (30 sensors/displays) | |
1 | × | DIYables Sensor Kit (18 sensors/displays) |
Additionally, some of these links are for products from our own brand, DIYables .
Overview of Rotary Encoder
A spinning knob called a rotary encoder can change twists into a signal. It shows how much something turned and where it is. There are two main kinds:
- Incremental encoder: It uses fast signals to see how much something moved.
- Absolute encoder: This type gives a unique code for each spot, which helps figure out exactly where something is, even if the power goes out.
This guide is all about the incremental encoder.
Rotary Encoder Module Pinout
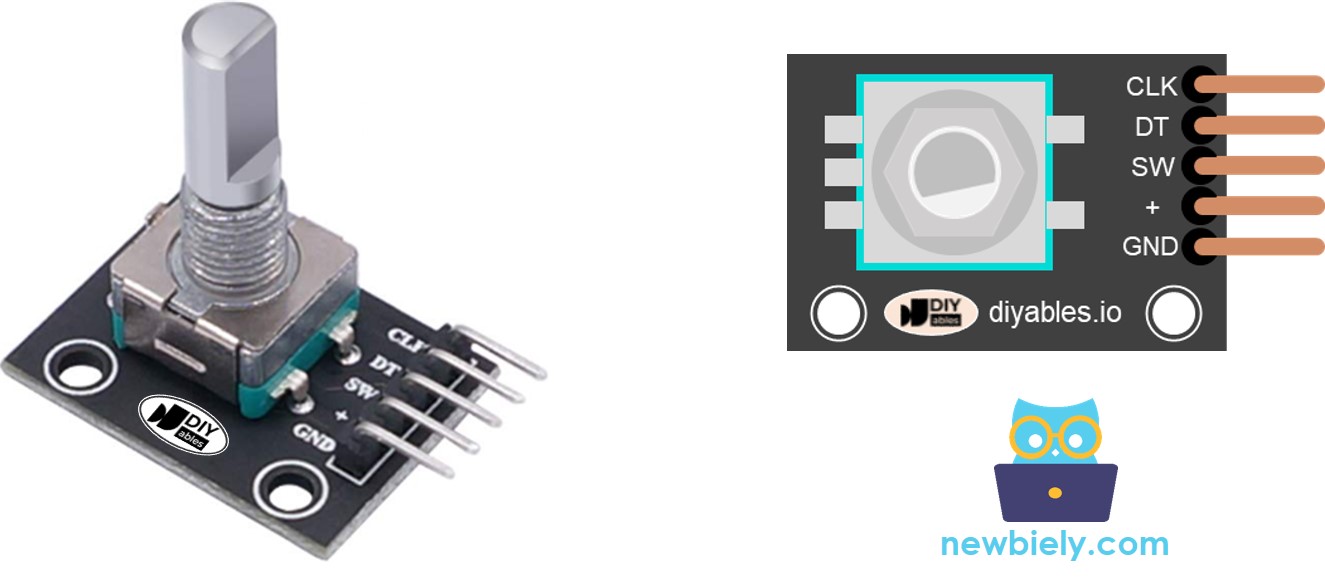
A rotary encoder module has 4 pins:
- CLK pin (Output A): is the main pulse that tells us how much rotation has occurred. Whenever you turn the knob by one detent (click) in either direction, the CLK pin outputs a signal that is a completes a full cycle (LOW → HIGH → LOW).
- DT pin (Output B): acts like the CLK pin but outputs a signal lags behind CLK signal by 90 degrees. It helps us figure out the direction of rotation (clockwise or anticlockwise).
- SW pin: is the output from the pushbutton inside the encoder. It’s normally open. If we use a pull-up resistor in this pin, the SW pin will be HIGH when the knob is not pressed, and LOW when it is pressed.
- VCC pin (+): needs to be connected to VCC (between 3.3 and 5 volts)
- GND pin: needs to be connected to GND (0V)
Rotary Encoder vs Potentiometer
You might confuse the rotary encoder with the potentiometer, but these are distinct parts. Here's a comparison between them:
- The rotary encoder can be thought of as the modern version of a potentiometer, but it offers more capabilities.
- The rotary encoder can spin all the way around without stopping, while the potentiometer can only rotate about three-quarters of the way.
- The rotary encoder gives out pulses, whereas the potentiometer produces analog voltage.
- When you only need to know how much the knob has moved without pinpointing its exact position, the rotary encoder is convenient. On the other hand, the potentiometer is valuable when you require precise knowledge of a knob's position.
How Rotary Encoder Works
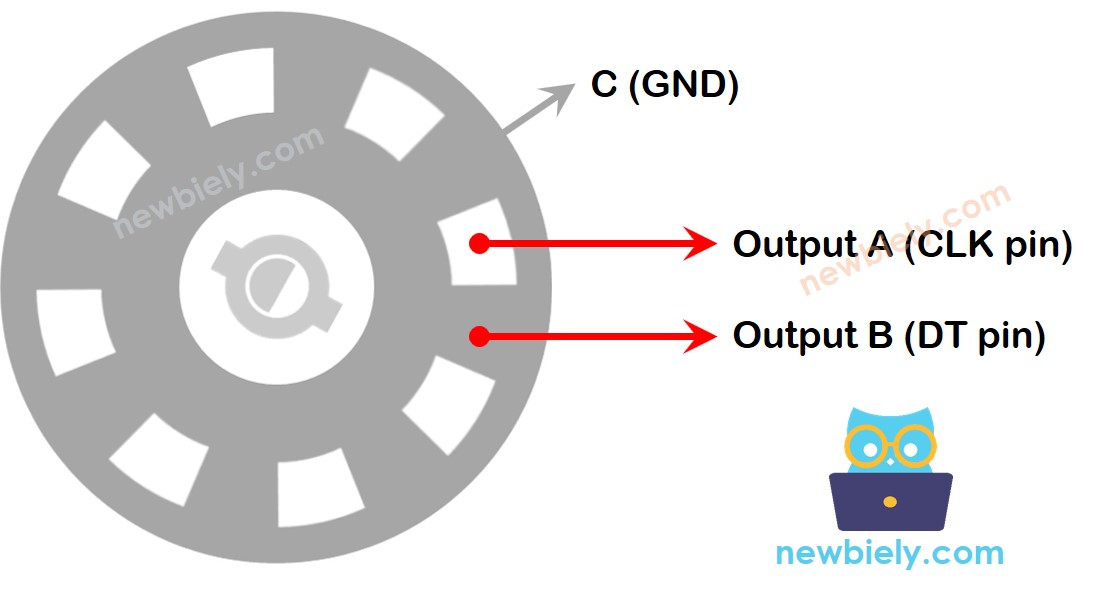
Inside the encoder, there's a disc with slots connected to a pin called C, which is like a shared ground. There are two more pins, A and B.
- When you twist the knob, pins A and B touch the shared ground pin C, but in a certain order depending on which way you turn the knob (clockwise or anticlockwise).
- These touches create two signals. They're a bit different in timing because one pin touches the ground before the other. Two signals are 90 degrees out of sync with each other. This is called quadrature encoding.
- When you turn the knob in clockwise direction, pin A touches the ground before pin B. When you turn the knob to the counterclockwise direction, pin B touches the ground before pin A.
- By monitoring when each pin touches or leaves the ground, we can figure out which way the knob is turning. We do this by checking what happens to pin B when pin A changes.
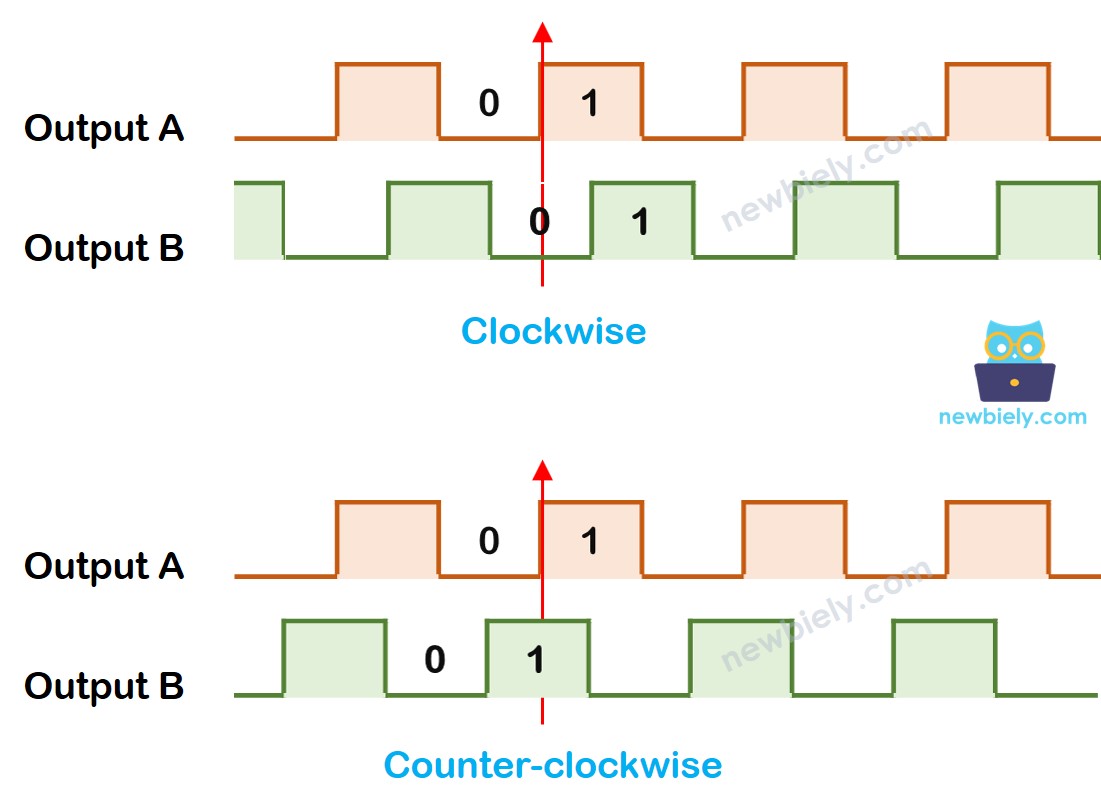
When A changes states from LOW to HIGH:
- If B is LOW, the knob is turned clockwise.
- If B is HIGH, the knob is turned anticlockwise.
※ NOTE THAT:
Pin A and B are connected to CLK and DT pins. However, depending on the manufacturers, the order may be different. The codes provided below are tested with the rotary encoder from DIYables
How To Program For Rotary Encoder
- Check the signal from CLK pin
- If the state changes from LOW to HIGH, check the state of the DT pin.
- If the state of the DT pin is HIGH, the knob is turned in the anticlockwise direction, increase the counter by 1
- If the state of the DT pin is LOW, the knob is turned in the clockwise direction, decrease the counter by 1
Wiring Diagram
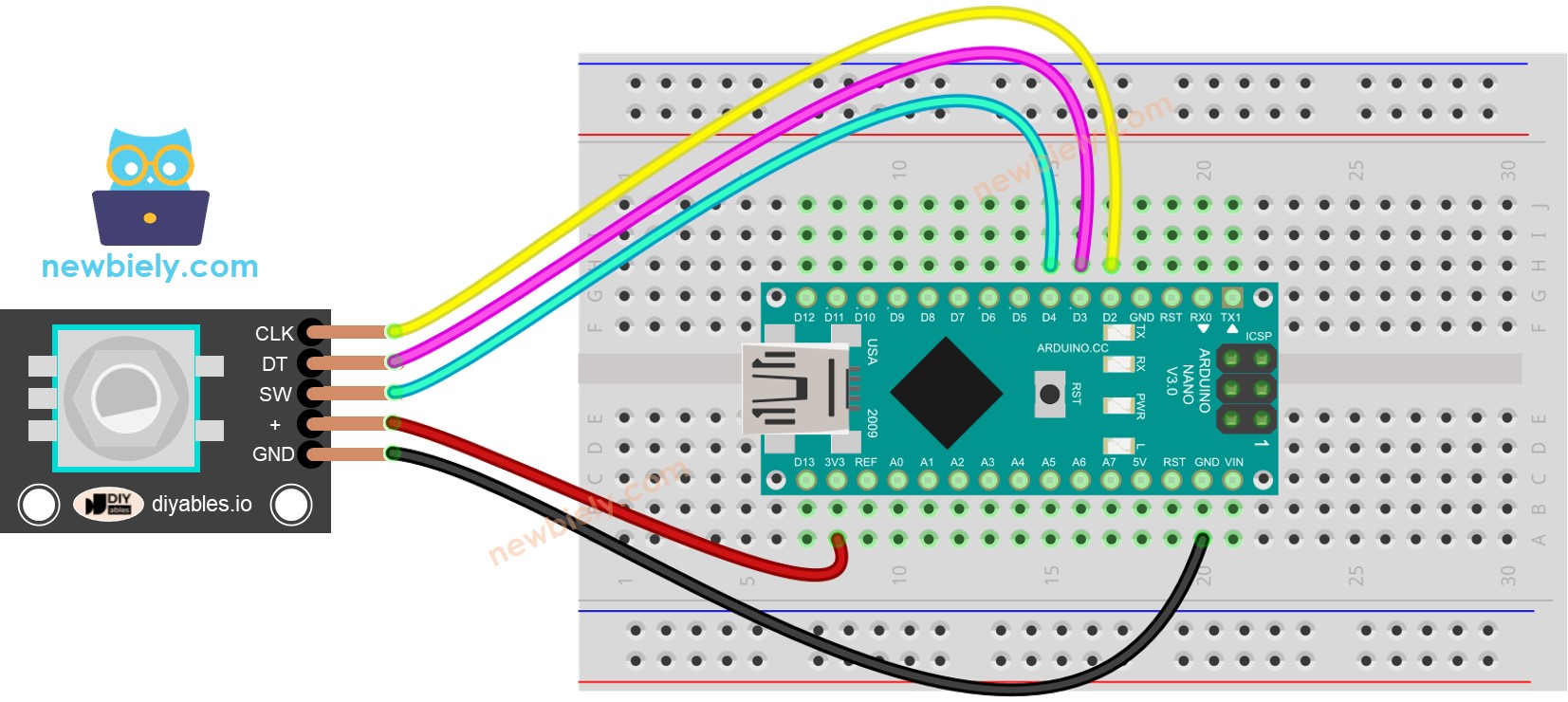
This image is created using Fritzing. Click to enlarge image
See The best way to supply power to the Arduino Nano and other components.
Arduino Nano Code – Rotary Encoder
The below Arduino Nano code does:
- Detects the direction and amount of rotation of the encoder.
- If detecting the knob turned by one detent (click) in clockwise direction, increase the counter by one.
- If detecting the knob turned by one detent (click) in anticlockwise direction, decrease the counter by one.
- Detects if the button is pressed.
To simplify the code for button debouncing, the ezButton library is used.
Detailed Instructions
- Install ezButton library on Arduino IDE. See How To
- Copy the above code and open with Arduino IDE
- Click Upload button on Arduino IDE to upload code to Arduino Nano
- Turn the knob in clockwise, then anticlockwise
- Press the knob
- Check out the result on the Serial Monitor.
Code Explanation
Check out the line-by-line comments in the code
Arduino Nano Code – Rotary Encoder with Interrupt
In the previous example code, we use the polling method, which continuously check the pin's state. This has two disadvantages:
- Waste Arduino Nano resource
- Some counter may be missed if another code takes long time to excecute.
One approach to handle this is by using interrupts. Interrupts eliminate the need for constant checking of a particular event. This allows the Arduino Nano to carry out other tasks without overlooking an event.
Here’s an example of how to read a rotary encoder with interrupts.
Now, As you twist the knob, you'll notice information appearing on the Serial Monitor, much like what you saw in the earlier code.
※ NOTE THAT:
- If you use the interrupt, you need to connect the encoder's CLK pin to an Arduino Nano pin that can handle interrupts. But remember, not all Arduino Nano pins can do this. For example, on the Arduino Nano, only pins 2 and 3 can work with interrupts.
- You might come across tutorials on other websites that use two interrupts for a single encoder, but this is unnecessary and wasteful. Just one interrupt is sufficient.
- It's important to use the volatile keyword for global variables used in the interrupt. Neglecting this could lead to unexpected issues.
- Keep the code within the interrupt as straightforward as you can. Avoid using Serial.print() or Serial.println() inside the interrupt.
Arduino Nano Rotary Encoder Application
With Rotary Encoder, we can do the following applications but not limit:
- Arduino Nano - Rotary Encoder controls Position of Sevo Motor
- Arduino Nano - Rotary Encoder controls Brightness of LED
- Arduino Nano - Rotary Encoder controls Speed of Stepper Motor